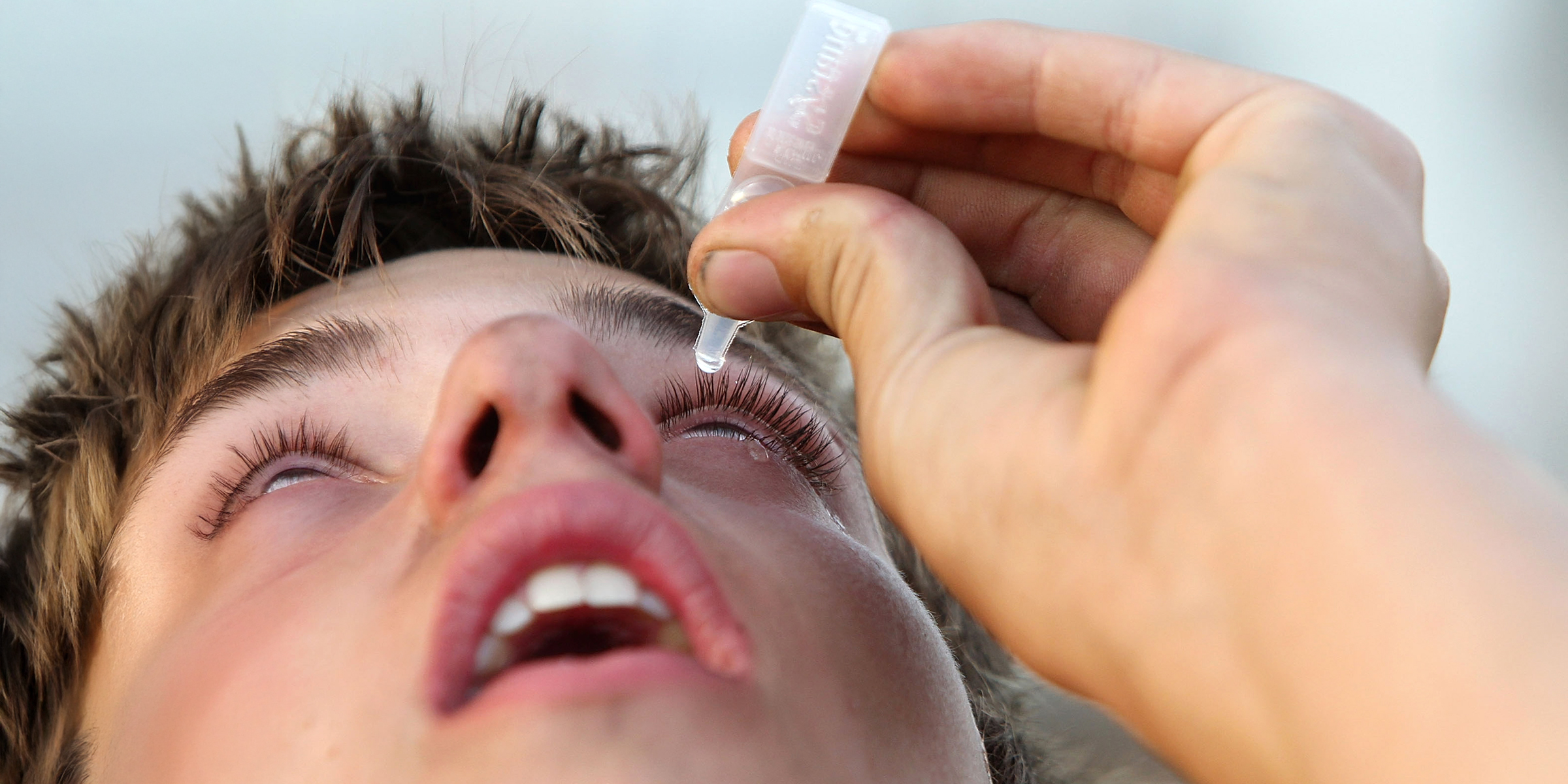
Recall Notice Issued for Over 75,000 Cases of Eye Care Products — Details
The Food and Drug Administration (FDA) has disclosed details about the specific batches of eye care products being recalled and has provided important information on manufacturing standards.
Recently, the U.S. Food and Drug Administration (FDA) and pharmaceutical company AvKARE have issued a recall notice for over 75,000 cases of eye care products. AvKARE has urged the public to discontinue use immediately and for retailers to remove the products from active inventory.
The recall, officially launched on April 23, 2025, was initiated voluntarily by BRS Analytical Services, LLC, a firm based in Saint Louis, Missouri. No formal press release accompanied the announcement. The FDA subsequently classified the event under ID 96741 and designated it as a Class II recall on May 6.
According to the agency, a Class II status indicates that use of or exposure to the recalled products may lead to temporary or medically reversible adverse health consequences, though the probability of serious harm is "remote."
Nonetheless, the scope of the recall is significant, as it applies to product batches distributed nationwide throughout the U.S. According to statements from both the FDA and AvKARE, the recall was prompted by deviations from Current Good Manufacturing Practice (CGMP) guidelines.
Specifically, deviations were discovered during an FDA audit, which raised serious concerns about the sterility of the affected eye care products. Sterility is especially crucial in ophthalmic solutions, and although the precise health risk to end users remains undetermined, AvKARE could not definitively rule out potential patient harm.
As a precautionary measure, the company has called for an immediate cessation of product use and urged retailers to remove the affected stock from shelves and online listings without delay.
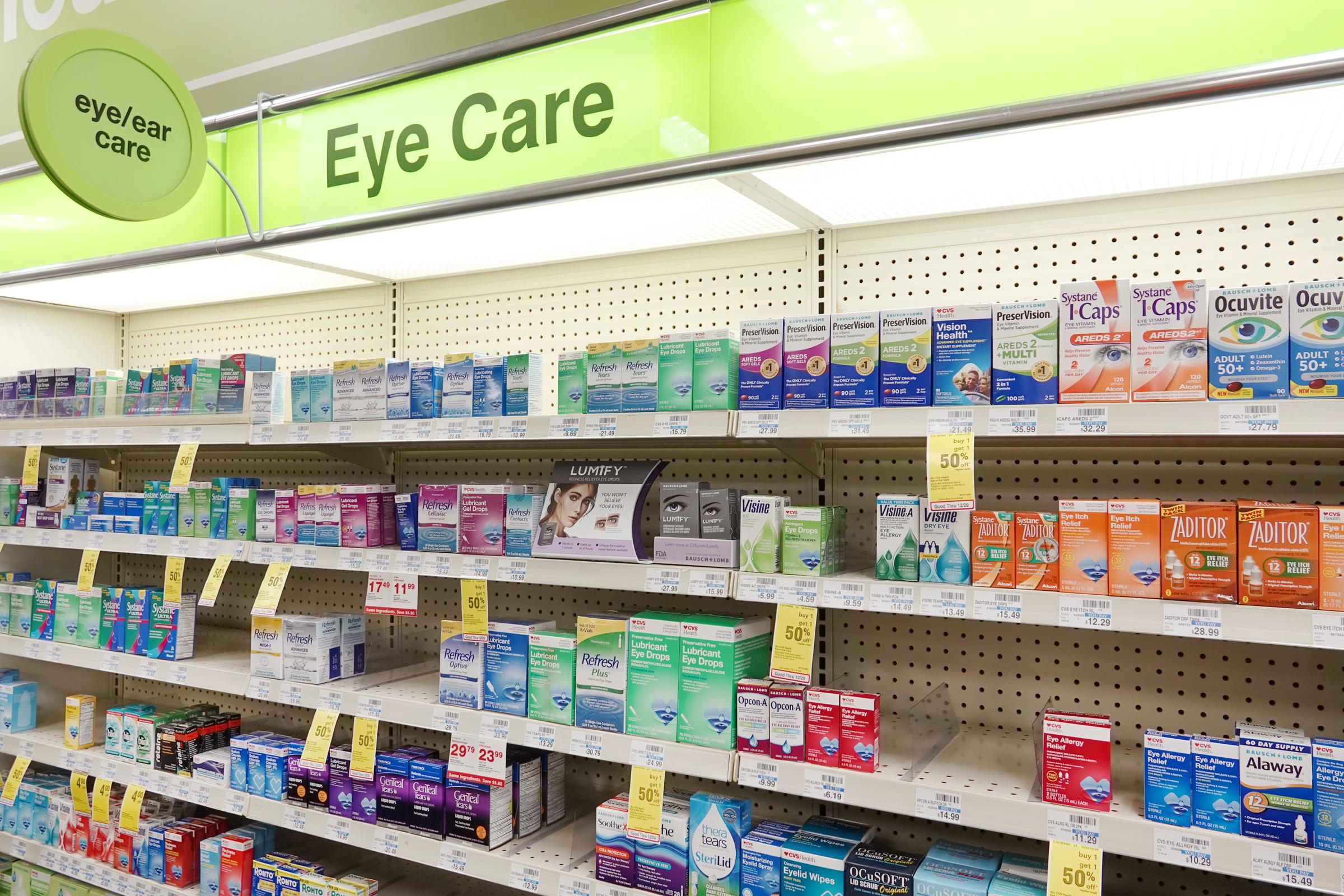
Eye care products on display at a CVS pharmacy; photo taken in 2018. | Source: Getty Images
The FDA echoed this recommendation, citing a lack of assurance that the products met the required standards for safe use. The recall involves five specific types of eye care formulations marketed under the AvKARE label.
These include Artificial Tears Ophthalmic Solution containing Dextran 70.01%, Glycerin 0.2%, and Hypromellose 0.3%; Carboxymethylcellulose Sodium Ophthalmic Gel 1%; Carboxymethylcellulose Sodium Ophthalmic Solution 0.5%; Lubricant Eye Drops Solution with Polyethylene Glycol 400 0.4% and Propylene Glycol 0.3%; and Polyvinyl Alcohol Ophthalmic Solution 1.4%.
Each of these products has been linked to CGMP deviations and a lack of sterility assurance. The total quantity affected varies per product, with Carboxymethylcellulose Sodium 0.5% Ophthalmic Solution accounting for the largest share at 32,876 cases.
This is followed by Polyvinyl Alcohol Solution at 14,333 cases; Artificial Tears at 13,872 cases, Lubricant Eye Drops at 13,104 cases, and the 1% Gel formulation at 1,610 cases.
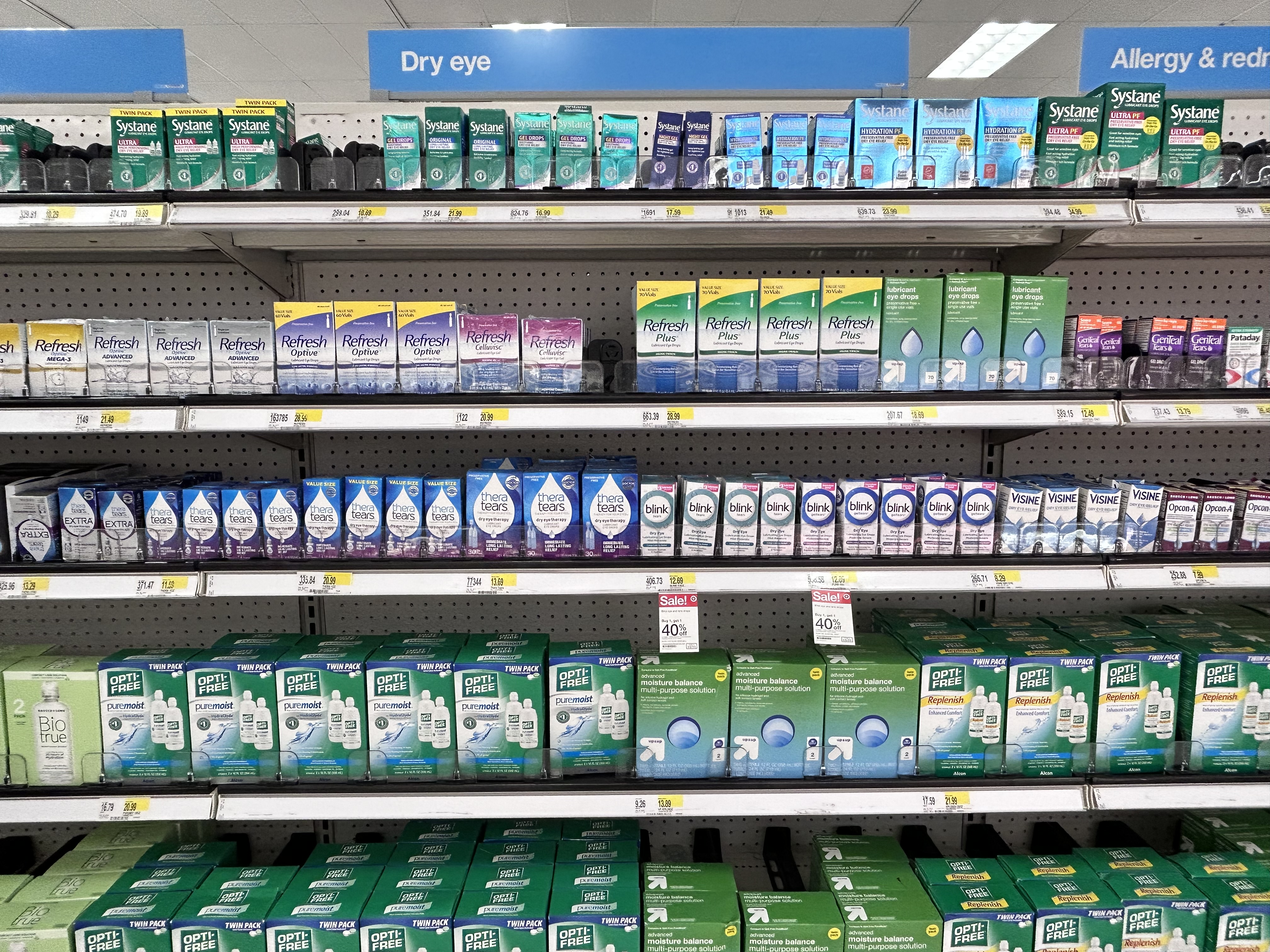
An eye drop aisle at a Target store in Queens, New York; photo taken in 2023. | Source: Getty Images
These products were initially shipped between May 26, 2023, and April 21, 2025. The affected lot codes span an even broader window, with some expiration dates extending to March 2027.
For instance, various lots of the Artificial Tears Ophthalmic Solution are set to expire between October 2025 and October 2026, while several batches of the Carboxymethylcellulose Sodium 0.5% solution are marked with expiration dates into January 2027.
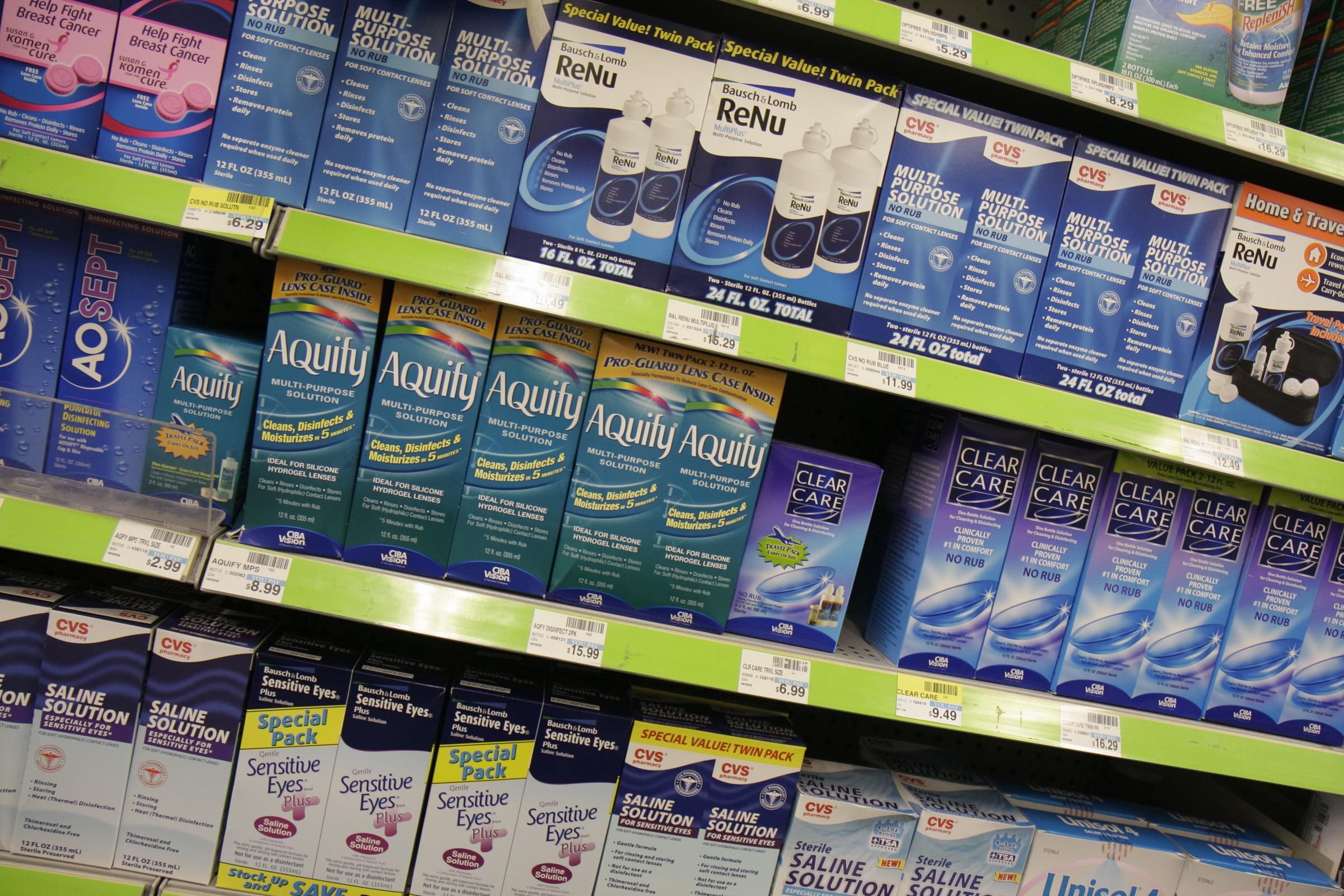
A photo of eye care products at a CVS pharmacy in 2009. | Source: Getty Images
AvKARE provided a detailed list of National Drug Codes (NDCs), lot numbers, and expiration ranges to aid in product identification. They have also urged consumers to review packaging closely to determine whether their product is included in the recall.
To assist in the return process, AvKARE has made a PDF version of the official recall notice available for download. Consumers and retailers are instructed to complete the "Quantity to Return" section and fax the form to 931-292-6229.
Alternatively, the company has provided the email address, customerservice@avkare.com, for electronic communication. All recalled products are to be shipped to R&S Northeast LLC, located at 8407 Austin Tracy Road, Fountain Run, Kentucky, 42133.
Packages must be clearly marked with the phrase "Ophthalmic RECALL" to ensure proper handling. AvKARE has assured full credit for all returns, including reimbursement for shipping costs, and expressed regret for any inconvenience caused.
While the recall notice itself has drawn national attention, it also underscores a larger issue within pharmaceutical manufacturing: The importance of strict compliance with the FDA's Current Good Manufacturing Practice standards.
Often referred to as CGMP, these regulations serve as the backbone of quality assurance in the drug industry, governing everything from facility oversight to the materials and methods used in production.
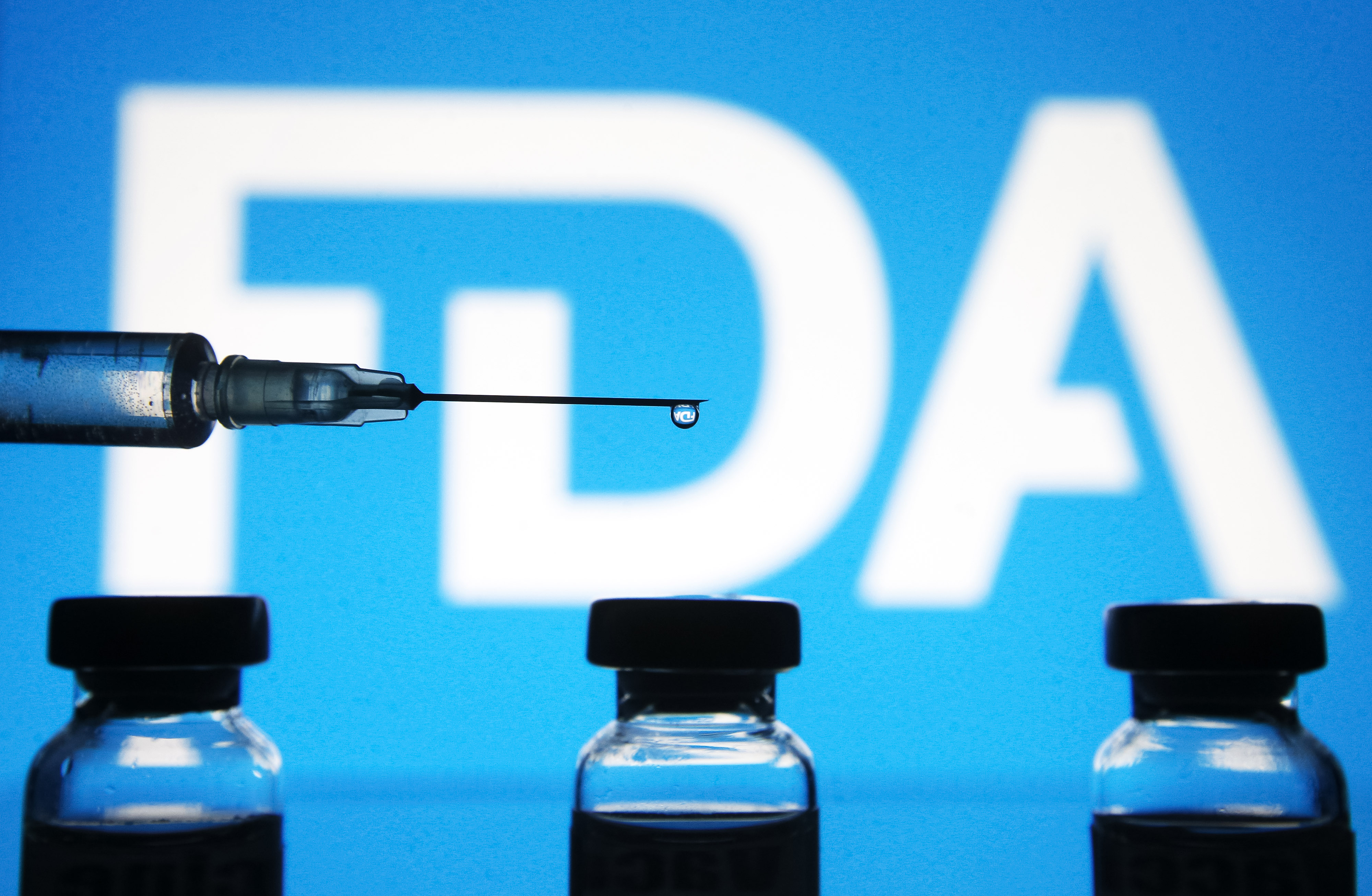
A photo of a medical syringe and vials in front of an FDA backdrop; photo taken in Ukraine on January 1, 2021. | Source: Getty Images
When followed properly, CGMP protocols ensure that medications are produced consistently and meet predetermined quality specifications for identity, strength, purity, and safety.
The FDA emphasizes that CGMP systems are not optional guidelines but essential safeguards built into the entire manufacturing process. These include maintaining clean and reliable facilities, sourcing high-quality raw ingredients, implementing stringent operational procedures, and running thorough, accountable laboratory testing.
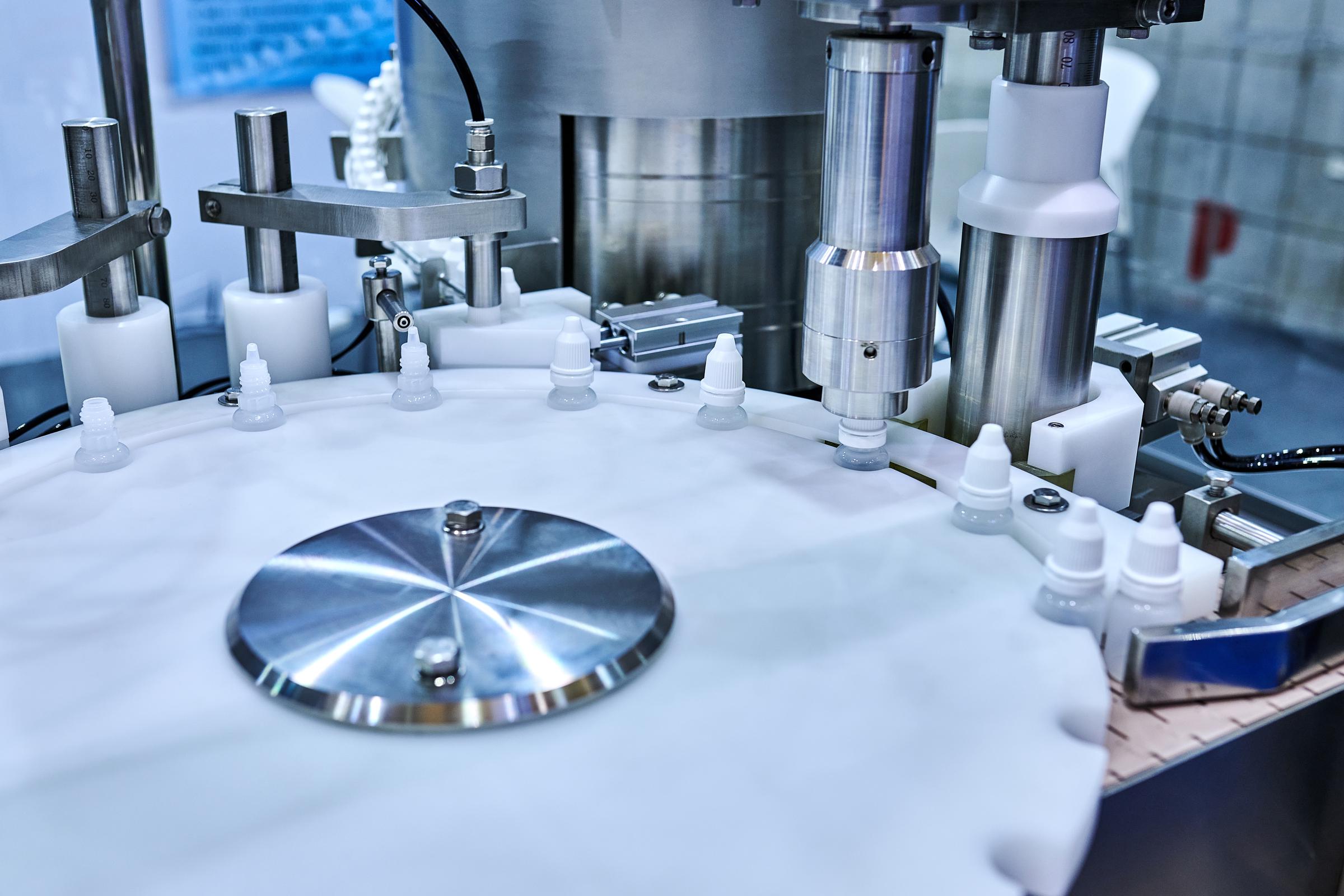
A photo showing the process of eye care product bottling. | Source: Getty Images
The ability to detect, investigate, and correct deviations before they impact the end product is equally critical. Without such measures, the risk of contamination, product mix-ups, or breakdowns in quality control can significantly increase.
Ultimately, CGMP aims to minimize errors before they reach the consumer, providing a formal system of checks and balances that protect public health.
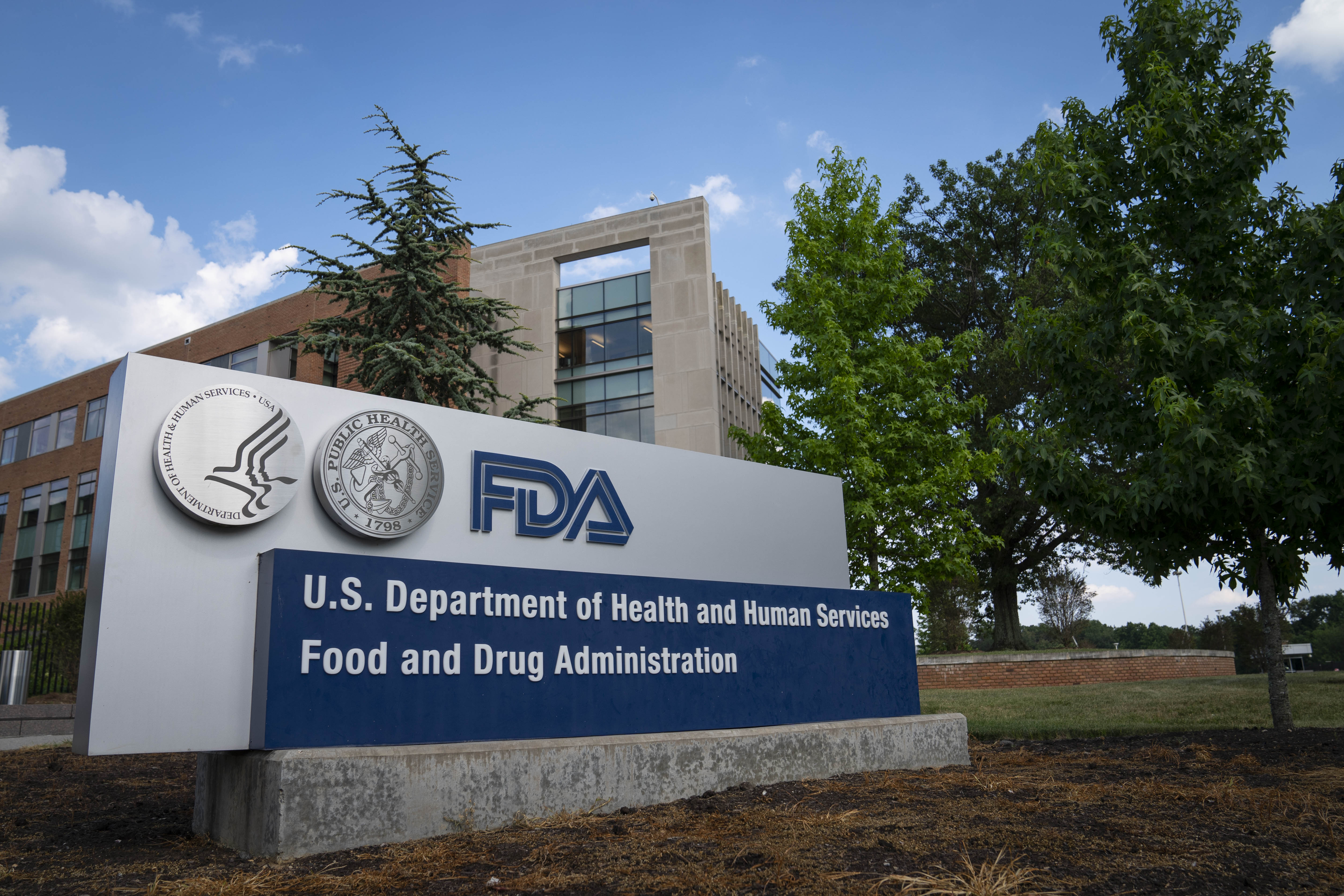
The FDA sign in front of the organization's headquarters in White Oak, Maryland on July 20, 2020. | Source: Getty Images
As this incident illustrates, even a single lapse in manufacturing integrity can trigger widespread consequences in logistics, consumer trust, and safety.
The FDA encourages industry professionals and the public to stay informed and vigilant, reinforcing the critical role that oversight and accountability play in ensuring the reliability of every drug that reaches a patient's hands.
The information in this article is not intended or implied to be a substitute for professional medical advice, diagnosis or treatment. All content, including text, and images contained on ondoho.com, or available through ondoho.com is for general information purposes only. ondoho.com does not take responsibility for any action taken as a result of reading this article. Before undertaking any course of treatment please consult with your healthcare provider.